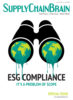
Visit Our Sponsors |
|
|
|
|
|
|
|
|
|
|
|
|
|
|
|
|
|
|
|
|
|
|
|
|
|
|
|
|
|
|
Recent research by PwC indicates that industrial manufacturing companies plan to invest 5 percent of annual revenue in digital operations solutions over the next five years. And they are setting themselves ambitious targets for the level of digitization and integration that can be achieved.
Many companies are already producing machines to deliver on the vision of the connected factory, using the power of the internet to link machines, sensors, computers and humans in order to enable new levels of information monitoring, collection, processing, and analysis. This is adding to the products and services that companies can offer their customers, helping them work in collaborative ways in the design of future machines and their digital environment to boost performance.
A number of technologies, including robotics, cobotics, 3D printing and nanotechnology, have direct relevance for many industrial manufacturing applications while other technologies, such as augmented reality, can enable manufacturers give customers real-time information and training at the point of use.
Some of these developments are maturing now. Others remain for the future. The rate of adoption of Industry 4.0 technologies by industrial manufacturing companies is accelerating fast.
The digitization, integration and automation opportunities offered enable companies to collaborate both internally and across their value chains in ways that can provide a step change in productivity as well as design and build quality. And they are opportunities that are increasingly important as companies seek to stay relevant as the era of digitally-connected smart infrastructure develops.
Source: PwC
RELATED CONTENT
RELATED VIDEOS
Timely, incisive articles delivered directly to your inbox.