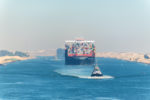
Visit Our Sponsors |
|
|
|
|
|
|
|
|
|
|
|
|
|
|
|
|
|
|
|
|
|
|
|
|
|
|
|
|
|
|
With this at stake, implementing IT strategies that reduce or eliminate unplanned downtime of critical manufacturing applications should be integral to lean program strategies. This often requires a change in mindset.
Most IT and operations people prepare for rapid recovery from failure, assuming it is inevitable. Instead, proactively preventing downtime from happening in the first place yields better outcomes; it's also more efficient in practice and cost-effective over the long term.
Read Full Article
Keywords: supply chain management IT, supply chain solutions, supply chain systems, lean initiatives in manufacturing, lean strategies
RELATED CONTENT
RELATED VIDEOS
Timely, incisive articles delivered directly to your inbox.