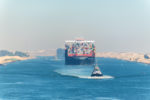
Visit Our Sponsors |
|
|
|
|
|
|
|
|
|
|
|
|
|
|
|
|
|
|
|
|
|
|
|
|
|
|
|
|
|
|
The emerging use of radio frequency identification (RFID) to locate and track goods in the supply chain is focusing increased attention and resources at the point of execution-the distribution centers, transport hubs and commercial vehicles on the "edge" of the enterprise. Terms likes "edgeware" and "edge infrastructure" are fast becoming part of the arcane vocabulary of the supply chain, even as many complain that it is pushing them to the "bleeding edge" of technology.
While central to this trend, RFID is only the latest breakthrough in an evolution that has been going on for 10 to 15 years, according to Bryan Tracey, chief architect at GlobeRanger, Richardson, Texas. First came computers in the warehouse, he says, followed by the introduction of mobile computing. "All of a sudden software was actually living on handheld devices that were a few inches from the products that were in motion, which meant that decisions could be made in near real time," he says. "Someone on the dock actually could see if something wasn't the right order because it was not in his handheld computer."
With the pervasive automation of RFID and other sensor technology, he continues, "we reach a point of intersection between the world of computing and the actual physical world where the two become essentially indistinguishable. So when we talk about the edge we are talking about the distribution of business logic both temporally and physically close to the point of action in the supply chain." GlobeRanger provides a leading edgeware platform, iMotion, which Tracey says enables companies to monitor and control edge devices, manage networks and transform data into actionable business information.
While edge infrastructure is not limited to RFID, it certainly is where all eyes are focused today. Mandates from the Department of Defense, Wal-Mart and other major retailers have started a march toward RFID adoption that few companies will escape. According to a survey last spring of 350 technology executives by BearingPoint, CIO magazine and the Software and Information Industry Association, 58 percent of respondents described RFID as "important" or "very important" to their company's business strategy. The same percentage expected to begin a trial or test project within the following 12 months, while 16 percent already had projects under way.
Momentum currently is being driven not only by mandates but also by progress in the development of standards. RFID in the supply chain passed a major milestone in December with ratification of a global standard for a UHF protocol defining how readers and tags talk to one another. This Generation Two air interface protocol, commonly known as Gen 2, was developed by more than 60 companies under the aegis of EPCglobal Inc., the standards organization entrusted with driving adoption of Electronic Product Code (EPC) technology. The electronic product code is the unique number that allows every tagged item to be identified individually instead of generically, as is the case with barcodes.
Gen 2 is important for a number of reasons. First, it provides a foundation upon which RFID infrastructure elements can be built, ensuring interoperability on a global scale. It also enables significant operational improvements over the Class 0 and Class 1/Gen1 readers and tags now in use with faster read rates and less susceptibility to interference. Additionally, security is improved by the use of advanced encryption technology, password protection and authentication.
Many hope that the biggest impact of Gen 2, however, will be mass production of the hardware needed to deploy an RFID infrastructure, especially tags, and a resulting decrease in price.
Even with the limited nature of pilot projects so far undertaken to test RFID in the supply chain, most users had anticipated that prices would be on the decline by this time. In some cases, a tag shortage has caused the opposite to happen. During a recent webcast sponsored by Consumer Goods Technology, one Wal-Mart supplier said his price for RFID tags was higher than it had been six months earlier, averaging 75 cents per tag. Other unconfirmed reports indicate that some suppliers are paying as much as $1.
With Gen 2, this situation is expected to improve. Texas Instruments and Philips Semiconductors, two major manufacturers that have been waiting for a ratified standard before entering the market, have indicated they now will ramp up production. It will be the second half of this year, however, before Gen 2 tags reach the market in any number.
"For us the challenge is to develop a UHF version of our tags," says Tony Sabetti, UHF/retail supply chain director for Texas Instruments RFid Systems, which already produces large quantities of different frequency RFID tags for other uses. "But our biggest challenge in manufacturing right now is in scaling from the hundreds of millions of tags we make today to the billions of tags we need to make tomorrow."
Just how fast demand will grow to billions of tags remains a big question mark. IDC Research, Framingham, Mass., estimates that RFID spending for the U.S. retail supply chain will increase from $91.5m in 2003 to nearly $1.3bn in 2008, including tags, infrastructure and systems integration. This figure is expected to reach $875m in 2007. RFID-related services will grow to about $270m in 2007 before leveling off, IDC projects, while software spending will not begin to grow until about 2006, when more companies will start to need RFID middleware.
Whatever the speed of adoption and investment turns out to be, most companies will eventually have to make a decision about RFID deployment. Understanding the elements of an RFID framework will enable them to look beyond mere compliance toward using the technology for competitive advantage.
RFID Framework
An RFID system consists of tags, printers, readers and middleware. Tags include a chip and an antenna embedded in a label. RFID printers simultaneously print labels and write to the electronic tag. Readers, which can be stationary or mobile, collect data from the tag and may apply a first level of intelligence, filtering out duplications and noise. Middleware turns the raw data into useable information and transmits it to back-end systems.
Tags are a large and recurring expense, which is why there is so much concern over their price. There also is concern over yield. Early trials generated complaints about tags that were dead on arrival or that failed to stand up to the rigors of a distribution environment. While acknowledging the existence of such problems, vendors say yield issues are being resolved.
Tag Technology
Scot Stelter, director of product marketing for Alien, a tag and reader manufacturer based in Morgan Hill, Calif., says a lot of the early failures were caused by tags, readers and printers that were not designed to work together. Such problems are common to any new technology, he says, and "going forward they are diminishing rapidly."
Most supply chain pilot programs use rolls of adhesive-backed paper shipping labels that are inlaid with a plastic-enclosed chip and antenna. The labels are printed and the tags encoded by an RFID-enabled printer in the warehouse before being attached to a case or pallet.
Converting RFID tags into printable labels is a multi-step process that has required a learning curve. "As we have learned more, the number of bad tags has gone down markedly," says Dan Bodnar, director of RFID at Intermec, a full-service provider of wireless data-collection solutions based in Everett, Wash. Bodnar notes that Intermec performs testing when the inlay is put into the label. "We are able to validate whether a tag is good or bad," he says. "We identify the bad tags; the printer will not print to them and the customer is not charged for them."
Many smart label printers, such as those from industry leader Zebra Technologies, Vernon Hills, Ill., also have this intelligence built in. "Our printer/encoders automatically void or reject a smart label or inlay that fails to respond properly to a reading or encoding instructions," says Matt Ream, general manager, RFID Systems. Zebra's integrated systems also offer the ability to write to tags outside the primary RFID printer and to verify that applied tags are correct by means of a downstream reader.
Sabetti of Texas Instruments blames the problem with poor tag yields on the fact that "most of the tags being shipped into the supply chain today are being shipped by startup companies that have no understanding of what is required to produce at Six Sigma quality levels." He says that TI has manufactured more than 100 million RFID tags for other industries with yields in excess of 99.7 percent. "There is nothing that would prevent us from achieving those same rates in supply chain applications."
![]() | |
"When we talk about the edge we are talking about the distribution of business logic both temporally and physically close to the point of action in the supply chain." - Bryan Tracey of GlobeRanger | |
RELATED CONTENT
RELATED VIDEOS
Timely, incisive articles delivered directly to your inbox.