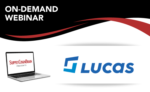
The last few years have seen a confluence of factors that can affect the supply chain. It’s become clear there’s no one clear “gotcha” moment that upset supply chain reliability, so much as an evolving systemic complexity.
The classic linear take on supply chain logistics was designed for a more stable world, with open borders and fewer restrictions on global trade. In today’s environment, however, the same method of operation can expose businesses to increased threats and interruptions along the supply chain.
In response, organizations are now collectively creating what Ernst & Young recently termed a “Great Supply Chain Reset.” The term recognizes the need for new processes and strategies for increased flexibility and the ability to capitalize on relationships, to create more sustainable and resilient operating environments. The systems required to make the shift are often more complex, so visibility, strong relationships and operational insight become vital to the success of a thriving supply chain.
Exploring “as-a-service” models, such as technology-enabled manufacturing applications, can be critical to success in this new era. For businesses looking to adopt them, it’s imperative to seek partners with on-demand production capabilities and the flexibility to handle production requirements for orders of all sizes, from prototype to full scale. By doing so, organizations can submit their designs for immediate prototyping and seamlessly adjust production quantities to match their needs in real time. They can also be connected with onshore or nearshore manufacturers capable of meeting their specifications without constraints. With the help of this technology, manufacturing becomes more efficient. It not only cuts down on waste, but also guarantees faster production times and the ability to grow or scale up as needed.
Key to this enhanced resilience is achieving a balance between nearshoring, reshoring and offshoring. A recent survey of 2,000 US and U.S. CEOs by Proxima made it clear: Nearshoring is here to stay as a cost-saving measure that strengthens the supply chain and wards against possible disruptions. Forty-three percent of CEOs surveyed have either already implemented or are planning to implement nearshoring or reshoring to improve operations, as opposed to 26% last year.
Physical proximity is among the many advantages of nearshoring. Shared time zones, cultural affinities and simplified communication channels all facilitate enhanced collaboration, while reducing the disruptions and complexities that are more likely in offshoring arrangements. Near- and reshoring arrangements also foster closer relationships, a key element in revitalizing the supply chain following successive years of shocks.
Genuine partnerships with suppliers can be realized through prioritizing seamless operations and flexibility over mere cost-cutting. An exclusive focus on line-item cost-cutting can often overlook the broader impact on the bottom line. Nearshoring, as a strategic supply chain approach, amplifies visibility, promotes transparency and enhances collaboration.
In charting a course within this evolving framework, it’s crucial to evaluate automation and transparency within a manufacturing partner's supply chain. By embracing automation, companies can harness the power of data-driven decision-making, minimize the potential for human error and ensure rigorous compliance.
As businesses consider potential manufacturing partners, those with powerful automation and transparency capabilities can be valuable allies in navigating the complexities of modern supply chain management.
The alterations currently taking place in global supply chains are far from being mere stopgap solutions. Instead, they represent a fundamental shift, a new paradigm reshaping the way businesses operate. This Great Supply Chain Reset isn’t a passing phase; it’s a permanent fixture in the business landscape. Companies that recognize this reality and adapt accordingly stand to gain significant advantages.
Businesses should view these changes as an opportunity, rather than a hindrance. Embracing the Great Supply Chain Reset allows companies to build greater resilience into their operations. That means being able to withstand and recover from disruptions, whether in the form of a global crisis, a sudden surge in demand or unforeseen logistical challenges. By actively adapting to this new paradigm, businesses can create a stronger and more agile business model.
Misha Govshteyn is chief executive officer of MacroFab.