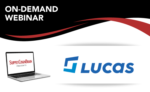
The methodology known as ESSA — for eliminate, simplify, standardize and automate — can help supply chains overcome an abundance of unusable technology as they pursue digital transformation.
Following is a closer look into the four components of the ESSA approach.
Eliminate removes non-value-added activities from any process. Say a procurement employee manually types vendor information into a system when they could automate that repetitive, time-consuming task. Their time is better spent negotiating with vendors and obtaining the best product or services rates. In the process, a non-value-added task is replaced by one that adds value.
Simplify involves making supply chain procedures more streamlined. Can steps be eliminated because they take too long to complete? Consider, for instance, a supply chain operations supervisor asking a team member to take the same raw data and create reports from five different viewpoints. This unnecessarily adds complexity and could be streamlined into one report, perhaps with five different introductions. If a 75-step core process can be shaved down to 20, then do so. Many large supply chain organizations, steeped in “this is the way we do things” thinking, can simplify processes, saving time and money.
Standardize aims to create and implement a uniform, repeatable pattern for completing a task, whether between departments, site locations, customers or suppliers. Sometimes referred to as business process standardization, it starts by pinpointing a scattered way in which a problem is being addressed — then creating a singular solution to be used organization-wide. Standardization is applicable for supply chains for everything from ensuring production quality control to maintaining equipment and managing vendor contracts.
Automate refers to using technology such as artificial intelligence and machine learning to perform supply chain processes with little to no human attention or effort involved. It might involve development of a vendor application programming interface (API), eliminating redundant work and freeing up staff to do more value-adding tasks.
ESSA can be applied to any company and industry. When it comes to the supply chain, advantages include improved agility and responsiveness, efficiency and cost savings, visibility and traceability, and worker skill development and job satisfaction.
ESSA addresses the problem of tech sprawl. Technology can benefit modern-day supply chains, but solutions shouldn’t be looked at as shiny new objects. The focus should be on those that actually improve business outcomes.
For example, a warehouse management system (WMS) can optimize distribution-center operations by automating tasks, providing real-time inventory visibility while processing orders more efficiently. And a data-management platform that connects with other technology provides visibility into labor, automates contractor compliance, and reduces common invoicing errors.
Reducing tech sprawl might involve finding a digital tool that integrates with multiple systems and does the job of several others.
While the ESSA methodology can usher in a host of benefits to supply chains, successful implementation requires planning, shifting gears, collaboration among participants, and the right technology support. It should also be adopted with all stakeholders, from the top down, working together to adopt process-enhancing methods.
Each supply chain is unique, and how companies go about adopting the ESSA approach will differ accordingly. What they have in common, however, is the need to replace manual processes with value-adding ones. ESSA has the power to turn ordinary actions into extraordinary results, when implemented consistently and by each employee.
Jackie Andre is senior director, contractor optimization with Management Controls.