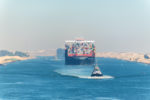
The first rule when it comes to any capital-intensive investment is to eliminate all possible alternatives that can be done with less friction. In the case of expanding your company’s warehouse, you should triage every available option before making a major commitment.
We should know; in the past few years we decided to both expand an existing location as well as break ground at entirely new locations. While the specific factors that influenced our decision may differ from your own calculus, the framework should look the same.
It's cheaper than building a new location. Setting aside everything else, it might be simpler to expand an existing structure, provided you own rather than lease it. The process of building a new location has added hurdles that can be avoided by expansion. Scouting out properties, deciding if it’s more feasible to buy an existing building versus buying land and designing and building one from scratch consume an immense amount of time and resources before a shovel even hits the ground.
Perhaps the simplest reason why warehouse expansion may not be an option is if there is no adjacent land available. If this is the case for your business, you have the option to look for new locations in strategically viable areas, or even consider outsourcing to a third-party logistics provider as a middle ground solution between expansion and selecting a new site.
You're transitioning to a different use. It may be that the original purpose of your warehouse suited the operational status quo of your business, but perhaps things have changed. If your warehouse was designed primarily for storage, yet an increasing proportion of inventory is moved via cross-docking, you may reach a point where it is no longer feasible to operate without expansion. To a certain degree, it is possible to restructure or redesign a warehouse based on changing needs; for example, you can rack over docks or build a mezzanine to add storage or pick and packing capabilities.
However, there are limitations to what is cost-effective or feasible without expansion, and a cost-benefit analysis may point to increasing your warehouse footprint as the smart move in the long run.
Using the storage to cross-docking example, it may be as simple as adding an additional dock door to keep inbound and outbound traffic flowing without the hazard and annoyance of pallets piling up in high-priority areas. Not enough dock doors can lead to delays when a truck is late, a team is running behind schedule, or there’s simply more inventory to load/unload than there are workers available to move it.
Expanding in this scenario requires little additional space to work with relative to the overall footprint of even a small warehouse, and has a hugely beneficial knock-on effect.
Your tech stack is at its limit. We’ve come a long way from the days of carbon copy paperwork and simple spreadsheets. Thanks to sophisticated demand forecasting software, warehouse management systems (WMS) that optimize workflow, and the addition of semi or fully-automated equipment to move inventory as quickly and efficiently as possible, you might have a hard time finding easy ways to improve day to day operations on the basis of technology.
Assuming that your warehouse deploys reasonably modern software that minimizes the inertia of factors related to slow-moving inventory or under-performing staff, if you want to increase your capacity to handle more inventory, expanding your warehouse might be your best bet.
That assumption may not hold true if your business has recently invested in a new WMS, inventory tool or other workflow improvement technology. A next-gen piece of software may make optimal use suggestions that can only be executed if you change your warehouse layout or size to improve picking speeds, for example. If your WMS is telling you to reorganize but you don’t currently have the space to do so, now is probably the time to expand (and ask yourself why you didn’t consider expansion as an associated cost while you were researching WMS).
You have commitments to honor. Of all the scenarios on this list, the one that makes the most clear-cut argument for warehouse expansion is if you have signed agreements with clients to provide an amount of storage beyond what you currently have capacity for. It’s a good problem to have, of course, but one that can only be addressed by adding more square footage. Either you buy a new warehouse location, you expand, or you lease more space to follow through.
What’s the right decision for you?
No matter what you decide, warehouse expansion will probably happen as effect rather than cause. It may be that your business model changes and you need to adapt your space accordingly. A new product that needs specialized handling or equipment that doesn’t fit in your current warehouse specs may become a bestseller and require the capital input to make the change.
Having a dedicated space for new processes will make it easier to test and adjust without disrupting the surrounding environment. If the new processes pay off, your business benefits from a better workspace and added real estate equity. While there is short term disruption due to construction as well as decreased cash flow, the long run benefits of expanding your warehouse seem to offer a strong upside to operations, with a built in hedge when viewed through the lens of in-demand real estate.
Jake Rheude is director of marketing for Red Stag Fulfillment.