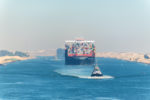
As the pandemic sent shockwaves through the global economy, the impact was felt across industries. Among the hardest hit sectors, the automotive industry experienced profound disruption, signaling the need for supply chain modernization.
Production shutdowns and the semiconductor shortage were just the beginning of it. Essential raw materials such as rubber, steel and aluminum have also been in short supply. Labor shortages, Trump-era tariffs, and the increasing frequency of severe weather events were among the compounding to further exacerbate the situation, resulting in longer lead times and catastrophic delays.
By late 2021, U.S. auto dealerships were equipped with only a fraction of the inventory available pre-pandemic. Meanwhile, mass-transit health concerns and government-stimulated consumer spending drove a spike in demand that couldn’t be met. While the end of the year is typically the auto industry’s peak selling season, eager consumers found it nearly impossible to purchase a new car as 2021 drew to a close. In the end, auto manufacturers sold fewer than 15 million new vehicles in 2021, well below the 17 million pre-pandemic industry average.
The ongoing health crisis has exposed critical auto supply chain vulnerabilities, presenting a pivotal opportunity for the industry and its suppliers to rethink inventory management. Technology adoption will be at the forefront of this transformation, with machine learning and artificial intelligence-based systems poised to deliver the greatest business impact.
AI offers three key advantages addressing core issues at the heart of supply chain failures: greater transparency, speed and predictive ability. With those objectives in mind, prioritizing the adoption of AI-powered technology is perhaps the single most impactful step that carmakers and OEMs can take to mitigate risks and improve auto supply chain resiliency.
Improved Transparency
Lack of visibility and access to data contributed to supply chain delays throughout 2021. Disparate systems and isolated silos of data hindered the flow of information, amplifying disruptions. When a critical component of an auto manufacturer’s assembly line breaks and is urgently needed, manufacturers generally don’t have reliable information about when that part will arrive. The question becomes whether it will arrive on time — or at all.
AI-based tools address this issue directly, streamlining information and making it more accessible to enable informed decision making. OEMs and carmakers are now relying on AI to enable full visibility into the shipping process, with real-time tracking that keeps tabs on a shipment’s precise location from the moment it leaves the warehouse. With access to an AI platform, all stakeholders are automatically notified of changes or delays.
Suppliers are also using AI to gain instant visibility into all available shipping methods, from the fastest options to the most economical. More information and visibility across the supply chain means less costly and time consuming back and forth. By improving visibility, AI is enabling better communication and integration capabilities, and helping industry decision makers to respond to shifting circumstances.
Faster Problem Solving
The pandemic underscored how important manufacturing agility and responsiveness is in the face of rapidly evolving situations. Rapid and informed decision-making is key. But in order to move quickly, stakeholders need to have data at their fingertips. With improved transparency, AI offers unparalleled speed. In addition to providing more data points and visibility, the technology can improve the decision-making process itself, minimizing human error.
AI streamlines activity across the supply chain. While traditional methods rely on phone calls and e-mails to coordinate an order, future-focused intelligent platforms can optimize every step of the process. Suppliers are already using AI to automatically provide real-time quotes for parts and services based on optimal routing and digital tariffs. In the instance of a downed production line, this can help restore assembly operations as quickly as possible.
Auto routing and direct dispatch further expedite the delivery process. AI also critically speeds reaction times, allowing logistics partners to respond instantly to traffic, weather delays and other travel issues, cutting troubleshooting time in half. Intelligent automation saves staff from being involved in these decisions, shortening the decision process.
As the automotive landscape evolves, suppliers will need to optimize at unprecedented speeds. Here, AI offers critical advantages as well. AI can learn from mistakes, evolving for better outcomes over a shorter period of time. When it comes to automotive logistics, for example, machine-learning systems will penalize a route in the event of a failure, noting the hiccup and logging the data to prevent that route from being utilized in future. By enabling greater efficiency across the auto supply chain, AI adoption is delivering improved return on investment.
More Accurate Predictions
To become more resilient, the industry must improve its ability to anticipate and plan for future disruptions. Today, most automotive manufacturers’ ability to predict manufacturing failures is limited. This leads to downed lines and costly disruptions that ripple throughout the supply chain. A single hour of unplanned downtime in a manufacturing line can result in hundreds of thousands of dollars in losses.
In an uncertain future, automotive success hinges on predictive prowess. It’s important to determine the likelihood of supply chain failures, and understand why they happen. AI is good at predicting things that people can’t, by avoiding human error and factoring historical data into the equation. It can instantly synthesize data on component usage and maintenance, and weigh that information against historical performance and parts lifespan to correctly assess the probability of supply chain failures.
AI can also more accurately anticipate transportation slowdowns before they happen. Machine learning can examine historical traffic data, driver performance, on-time departure percentages and weather patterns, to predict the best possible shipping route.
The ongoing health crisis revealed shortcomings in existing auto supply chain structures, placing the industry’s “just-in-time'' (JIT) manufacturing model under intense scrutiny. Designed to reduce inventory and minimize surplus with lean raw material and work-in-process inventories, the JIT model quickly buckled under the strain of pandemic-induced disruptions and increased consumer demand. The resilience of cross-continental supply lines and global interdependencies was called into question.
To reduce sensitivity to global conditions, the industry is beginning to consider reshoring of manufacturing and supply chains back to the U.S. It’s also looking to expand local warehousing, to anticipate the need for storing more parts. But reshoring manufacturing and localizing operations are only part of the solution. Carmakers will continue to need to minimize production costs, which means that some parts of the supply chain are likely to remain in distant yet economically advantageous locations.
It’s in the automotive industry’s best interest to reorient priorities around the adoption of AI technologies that can drive improvements across key facets of the supply chain. Auto manufacturing is at a critical crossroads; it’s time to evolve and fully utilize data and AI to streamline and optimize performance. Offering total transparency, rapid problem-solving and predictive accuracy, AI-supported logistics are poised to deliver on those priorities, propelling the automotive industry into a more intelligent and resilient future.
Ryan Rusnak is chief technology officer with Airspace.
As the pandemic sent shockwaves through the global economy, the impact was felt across industries. Among the hardest hit sectors, the automotive industry experienced profound disruption, signaling the need for supply chain modernization.
Production shutdowns and the semiconductor shortage were just the beginning of it. Essential raw materials such as rubber, steel and aluminum have also been in short supply. Labor shortages, Trump-era tariffs, and the increasing frequency of severe weather events were among the compounding to further exacerbate the situation, resulting in longer lead times and catastrophic delays.
By late 2021, U.S. auto dealerships were equipped with only a fraction of the inventory available pre-pandemic. Meanwhile, mass-transit health concerns and government-stimulated consumer spending drove a spike in demand that couldn’t be met. While the end of the year is typically the auto industry’s peak selling season, eager consumers found it nearly impossible to purchase a new car as 2021 drew to a close. In the end, auto manufacturers sold fewer than 15 million new vehicles in 2021, well below the 17 million pre-pandemic industry average.
The ongoing health crisis has exposed critical auto supply chain vulnerabilities, presenting a pivotal opportunity for the industry and its suppliers to rethink inventory management. Technology adoption will be at the forefront of this transformation, with machine learning and artificial intelligence-based systems poised to deliver the greatest business impact.
AI offers three key advantages addressing core issues at the heart of supply chain failures: greater transparency, speed and predictive ability. With those objectives in mind, prioritizing the adoption of AI-powered technology is perhaps the single most impactful step that carmakers and OEMs can take to mitigate risks and improve auto supply chain resiliency.
Improved Transparency
Lack of visibility and access to data contributed to supply chain delays throughout 2021. Disparate systems and isolated silos of data hindered the flow of information, amplifying disruptions. When a critical component of an auto manufacturer’s assembly line breaks and is urgently needed, manufacturers generally don’t have reliable information about when that part will arrive. The question becomes whether it will arrive on time — or at all.
AI-based tools address this issue directly, streamlining information and making it more accessible to enable informed decision making. OEMs and carmakers are now relying on AI to enable full visibility into the shipping process, with real-time tracking that keeps tabs on a shipment’s precise location from the moment it leaves the warehouse. With access to an AI platform, all stakeholders are automatically notified of changes or delays.
Suppliers are also using AI to gain instant visibility into all available shipping methods, from the fastest options to the most economical. More information and visibility across the supply chain means less costly and time consuming back and forth. By improving visibility, AI is enabling better communication and integration capabilities, and helping industry decision makers to respond to shifting circumstances.
Faster Problem Solving
The pandemic underscored how important manufacturing agility and responsiveness is in the face of rapidly evolving situations. Rapid and informed decision-making is key. But in order to move quickly, stakeholders need to have data at their fingertips. With improved transparency, AI offers unparalleled speed. In addition to providing more data points and visibility, the technology can improve the decision-making process itself, minimizing human error.
AI streamlines activity across the supply chain. While traditional methods rely on phone calls and e-mails to coordinate an order, future-focused intelligent platforms can optimize every step of the process. Suppliers are already using AI to automatically provide real-time quotes for parts and services based on optimal routing and digital tariffs. In the instance of a downed production line, this can help restore assembly operations as quickly as possible.
Auto routing and direct dispatch further expedite the delivery process. AI also critically speeds reaction times, allowing logistics partners to respond instantly to traffic, weather delays and other travel issues, cutting troubleshooting time in half. Intelligent automation saves staff from being involved in these decisions, shortening the decision process.
As the automotive landscape evolves, suppliers will need to optimize at unprecedented speeds. Here, AI offers critical advantages as well. AI can learn from mistakes, evolving for better outcomes over a shorter period of time. When it comes to automotive logistics, for example, machine-learning systems will penalize a route in the event of a failure, noting the hiccup and logging the data to prevent that route from being utilized in future. By enabling greater efficiency across the auto supply chain, AI adoption is delivering improved return on investment.
More Accurate Predictions
To become more resilient, the industry must improve its ability to anticipate and plan for future disruptions. Today, most automotive manufacturers’ ability to predict manufacturing failures is limited. This leads to downed lines and costly disruptions that ripple throughout the supply chain. A single hour of unplanned downtime in a manufacturing line can result in hundreds of thousands of dollars in losses.
In an uncertain future, automotive success hinges on predictive prowess. It’s important to determine the likelihood of supply chain failures, and understand why they happen. AI is good at predicting things that people can’t, by avoiding human error and factoring historical data into the equation. It can instantly synthesize data on component usage and maintenance, and weigh that information against historical performance and parts lifespan to correctly assess the probability of supply chain failures.
AI can also more accurately anticipate transportation slowdowns before they happen. Machine learning can examine historical traffic data, driver performance, on-time departure percentages and weather patterns, to predict the best possible shipping route.
The ongoing health crisis revealed shortcomings in existing auto supply chain structures, placing the industry’s “just-in-time'' (JIT) manufacturing model under intense scrutiny. Designed to reduce inventory and minimize surplus with lean raw material and work-in-process inventories, the JIT model quickly buckled under the strain of pandemic-induced disruptions and increased consumer demand. The resilience of cross-continental supply lines and global interdependencies was called into question.
To reduce sensitivity to global conditions, the industry is beginning to consider reshoring of manufacturing and supply chains back to the U.S. It’s also looking to expand local warehousing, to anticipate the need for storing more parts. But reshoring manufacturing and localizing operations are only part of the solution. Carmakers will continue to need to minimize production costs, which means that some parts of the supply chain are likely to remain in distant yet economically advantageous locations.
It’s in the automotive industry’s best interest to reorient priorities around the adoption of AI technologies that can drive improvements across key facets of the supply chain. Auto manufacturing is at a critical crossroads; it’s time to evolve and fully utilize data and AI to streamline and optimize performance. Offering total transparency, rapid problem-solving and predictive accuracy, AI-supported logistics are poised to deliver on those priorities, propelling the automotive industry into a more intelligent and resilient future.
Ryan Rusnak is chief technology officer with Airspace.