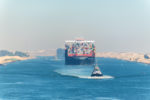
Workforce management in manufacturing, or any other business sector across the supply chain, is a juggling act for business leaders and human-resources professionals.
Now more than ever, worksites are carefully and simultaneously managing scheduling shifts, and helping to ensure worker safety by tracking workforce management to improve their ability to adhere to amplified health and safety regulations.
Many organizations are relying on business contingency plans to address new and evolving health and safety regulations as they occur, which can leave gaps in key processes and expose companies to a variety of compliance risks. As businesses enter the next phase of normalcy, it’s imperative that they continue to protect workers and reduce potential disruptions to the supply chain by enhancing standard operating procedures.
As manufacturers wrestle with budget constraints during the pandemic, workforce management reduces worksite risks and addresses costs as well. Specifically, workforce management systems:
- Decrease mistakes. Spreadsheets, manual timeclocks, and paper time sheets are ripe for human error. Automation of workforce-management functions makes mistakes much less likely. Accurate timekeeping can improve employee productivity and organizational profitability.
- Enhance efficiency. HR and payroll professionals are already dealing with unprecedentedly complex workloads. Automated workforce-management features can lighten administrative burdens by reducing payroll processing time, streamlining benefits and enrollment, and simplifying labor-management processes. A reduction in these time-consuming tasks frees HR staff to concentrate on the bigger picture.
- Maintain compliance. Automation of workforce management enables the tracking and recording of temperature checks (if applicable), and guarantees that capacity levels are being adhered to. By investing in a workforce-management solution, employers are outsourcing their compliance risk. They can rely on expert-led technology to apply the appropriate calculations at the correct times.
- Reduce physical contact. Touch-free workforce-management solutions reduce the risk of transmission of viruses such as COVID-19 and the flu. When paired with additional safety and wellness technology to measure employee distancing and interactions, organizations can optimize workspace layouts efficiently, to ensure that measures are keeping workers safe without hindering production.
- Provide health-screening devices. Employers now have the option to implement temperature-screening devices directly within their timeclocks, but should choose a system that doesn’t store or display temperature information, as it would expose the employer to possible HIPAA litigation.
During the pandemic, being flexible with shift scheduling has become critical to adhering to social-distancing protocols. That’s easier said than done, though. Given the scheduling complexities of manufacturing, it’s vital to open the channels of communication and rely on solid automation.
Without a clear-cut strategy for scheduling shifts, possibly on an around-the-clock basis, a supply chain runs into delays, fails to adhere to union rules, or jeopardizes the lives of workers. For example, employees scheduled to work at a specific job for which they’re not qualified are at risk for their own safety as well as that of others.
Aside from making sure the right people are in the right roles, an effective shift-scheduling strategy can involve incorporating staggered shifts, ample break times or extended work hours.
So how can business leaders address these new challenges? One way might be to institute rules-based scheduling through an automated tool that features a customizable dashboard. With this technology, an organization’s scheduling system can automatically take into consideration required certifications and skills, then schedule employees who meet those requirements. Furthermore, automation makes it easier to follow state, local, federal, and union rules that apply to a specific organization.
Scheduling technology also can help guarantee that each shift is properly staffed with qualified workers that meet staffing regulations. A rules-based scheduling tool limits overtime and fills gaps caused by illness or absence. In the end, it assists manufacturing sites by avoiding over- or under-scheduling, minimizing costs and turnover, and maximizing productivity and employee satisfaction.
Workforce-management systems with employee notifications keep every employee in the loop, easing the impact of last-minute schedule changes and ultimately helping retain the best workers by decreasing the interruption of their professional and personal lives. Notifications allow employees to manage childcare and transportation, while complying with labor laws of cities and states.
While scheduling can be a difficult balance, using automated, customizable scheduling software can keep an organization on track with shifts that are well-staffed with qualified, satisfied people.
Protecting workers and reducing health and safety compliance risks can improve a company’s ability to grow after a turbulent year. By using a workforce-management system, organizations can enhance policies and reduce potential disruption to the supply chain.
Jenna Dobrovolny is group product manager at Ascentis.