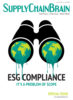
A growing commitment from automotive startups and legacy players is setting up the electric vehicle market for an exciting future. Tesla Inc., Ford Motor Co. and General Motors Co. have all announced plans to electrify their fleets as early as 2030.
But to gain a stable footing over competitors, western automakers — and policymakers — are keeping a close eye on China’s dominance over the critical mineral market.
By 2030, analysts from Benchmark Mineral Intelligence say that China will account for 65.4% of battery capacity, compared to 11.9% in North America and 19% in Europe.
Supply chain bottlenecks are forcing automakers to either extend delivery times for critical materials meant for EV battery production or delay their production plans entirely. To compete with China, automakers must look inward and find domestic sources of critical minerals to help compete with China’s growing foothold over the EV space.
It is time to usher in a widespread EV adoption and establish a prominent foothold on this new market. For that adoption of EVs to take off, the U.S. and western nations must first secure their domestic critical mineral industries. China is fast making moves in the EV landscape, quickly cementing themselves as industry leaders with automakers committing to an all-electric future. To remain competitive, the U.S. and other western nations must turn to localized supply chains that free themselves of restrictive shipping concerns, relieve supply chain bottlenecks, and ensure environmentally sustainable raw material sourcing operations take place.
Shipping, Storage Concerns
Supply chain constraints are not going away anytime soon. Experts have called a “normal” supply chain unlikely for most of 2022, with bottlenecks forming around ports, warehouses, and labor. For example, the Port of Long Beach, one of the largest container ports in the U.S., had a record breaking 2021, moving 9.38 million cargo containers. For automakers looking to build out their inventory of EVs, a backlog of critical minerals and necessary battery inputs will only exacerbate slowdowns and delays.
Shipping is expensive, and when coupled with a once-and-a-lifetime pandemic, you have a recipe for slow and inefficient battery production. Relying on shorter supply routes and domestic sourcing of critical battery materials will allow automakers to turn towards domestic partners for faster (and greener) battery production.
Storage concerns are another downside to the current supply chain crisis and automakers looking to utilize raw materials for their EV batteries stand to lose valuable critical materials to decay. Although elemental properties of battery grade sulfates do not dramatically change over time, storage can disrupt and alter their physical properties. Battery materials stored over long periods risk liquefaction and caking, both of which make handling more difficult.
ESG and Labor Benefits
Investing in environmentally sustainable raw material sourcing will help build strong brands and allow western nations to compete with an established Asian supply chain. Localized supply chains are more reliable and have a lower environmental footprint, which goes to the heart of what zero emission vehicles are all about. By shifting critical mineral supplies closer to home, automakers and western governments can react more quickly to disruptions, becoming more agile in their response and less impacted by geopolitical events like trade wars. This will bolster a homegrown and robust domestic workforce, while ensuring the most rigorous sustainable standards are followed.
With investments in the development of an integrated supply chain in the west, automakers stand to benefit, bringing employment, technology, and economic benefits to western nations and auto companies. As automakers move to an electric fleet, localized battery mineral sourcing will also help bring back jobs, creating an opportunity to boost an emerging industry with safe and reliable employment opportunities. These new positions will help boost western workforces with new options for environmentally safe and secure battery production.
To compete with China, western nations and manufacturers must look inward to secure domestic critical battery materials to help strengthen local economies, bring back jobs lost overseas, and establish a more robust and less wasteful carbon footprint. The future is bright for EV production and governments, automakers, and suppliers can all play a part in boosting a reliable, home-grown product.
Trent Mell is CEO of Electra Battery Materials.
A growing commitment from automotive startups and legacy players is setting up the electric vehicle market for an exciting future. Tesla Inc., Ford Motor Co. and General Motors Co. have all announced plans to electrify their fleets as early as 2030.
But to gain a stable footing over competitors, western automakers — and policymakers — are keeping a close eye on China’s dominance over the critical mineral market.
By 2030, analysts from Benchmark Mineral Intelligence say that China will account for 65.4% of battery capacity, compared to 11.9% in North America and 19% in Europe.
Supply chain bottlenecks are forcing automakers to either extend delivery times for critical materials meant for EV battery production or delay their production plans entirely. To compete with China, automakers must look inward and find domestic sources of critical minerals to help compete with China’s growing foothold over the EV space.
It is time to usher in a widespread EV adoption and establish a prominent foothold on this new market. For that adoption of EVs to take off, the U.S. and western nations must first secure their domestic critical mineral industries. China is fast making moves in the EV landscape, quickly cementing themselves as industry leaders with automakers committing to an all-electric future. To remain competitive, the U.S. and other western nations must turn to localized supply chains that free themselves of restrictive shipping concerns, relieve supply chain bottlenecks, and ensure environmentally sustainable raw material sourcing operations take place.
Shipping, Storage Concerns
Supply chain constraints are not going away anytime soon. Experts have called a “normal” supply chain unlikely for most of 2022, with bottlenecks forming around ports, warehouses, and labor. For example, the Port of Long Beach, one of the largest container ports in the U.S., had a record breaking 2021, moving 9.38 million cargo containers. For automakers looking to build out their inventory of EVs, a backlog of critical minerals and necessary battery inputs will only exacerbate slowdowns and delays.
Shipping is expensive, and when coupled with a once-and-a-lifetime pandemic, you have a recipe for slow and inefficient battery production. Relying on shorter supply routes and domestic sourcing of critical battery materials will allow automakers to turn towards domestic partners for faster (and greener) battery production.
Storage concerns are another downside to the current supply chain crisis and automakers looking to utilize raw materials for their EV batteries stand to lose valuable critical materials to decay. Although elemental properties of battery grade sulfates do not dramatically change over time, storage can disrupt and alter their physical properties. Battery materials stored over long periods risk liquefaction and caking, both of which make handling more difficult.
ESG and Labor Benefits
Investing in environmentally sustainable raw material sourcing will help build strong brands and allow western nations to compete with an established Asian supply chain. Localized supply chains are more reliable and have a lower environmental footprint, which goes to the heart of what zero emission vehicles are all about. By shifting critical mineral supplies closer to home, automakers and western governments can react more quickly to disruptions, becoming more agile in their response and less impacted by geopolitical events like trade wars. This will bolster a homegrown and robust domestic workforce, while ensuring the most rigorous sustainable standards are followed.
With investments in the development of an integrated supply chain in the west, automakers stand to benefit, bringing employment, technology, and economic benefits to western nations and auto companies. As automakers move to an electric fleet, localized battery mineral sourcing will also help bring back jobs, creating an opportunity to boost an emerging industry with safe and reliable employment opportunities. These new positions will help boost western workforces with new options for environmentally safe and secure battery production.
To compete with China, western nations and manufacturers must look inward to secure domestic critical battery materials to help strengthen local economies, bring back jobs lost overseas, and establish a more robust and less wasteful carbon footprint. The future is bright for EV production and governments, automakers, and suppliers can all play a part in boosting a reliable, home-grown product.
Trent Mell is CEO of Electra Battery Materials.