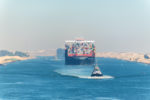
In the past few years, organizations have responded to a series of supply chain shocks mostly by employing isolated risk-mitigation strategies within planning, direct materials or manufacturing — typically without knowing what’s happening in the entire supply chain. This approach simply won’t work in today’s world of disruptions.
The supply chain of the future has clear visibility and is collaborative. Organizations will need to understand the state of the supply chain in real time, while aligning cross-functionally to reduce ad-hoc firefighting. Both efforts are critical to moving from short-term react-and-respond to a predict-and-manage approach, aimed at mitigating future supply chain issues more effectively.
These main functional areas — planning, direct materials, and manufacturing — are directly responsible for continuity of supply, and generally respond to disruptions by deploying an independent set of mitigating actions. However, when they address problems in isolation, they’re only solving an immediate problem and, in fact, are likely exacerbating future supply chain issues and trapping the organization in a never-ending react-and-respond cycle.
Planning
Historically, continuity of supply has meant executing a just-in-time (JIT) model and focusing on on-time-in-full (OTIF) measurements. Yet while this model had historically been efficient, it challenges planning’s ability to manage risk by constraining the amount of inventory and safety stock at the buying organization locations. Part of planning mitigation revolves around improving forecast accuracy and using longer horizons, as well as adjusting its own inventory carrying practices — for example, allowing for more days of on-hand inventory.
Planning is greatly affected by demand fluctuation, supply shortages, reduced capacity and labor. During a disruption or market event, it can respond by adjusting the material schedule and build plan to meet capacity, or smooth the demand plan to mitigate capacity and supply risk. But this will only continue the endless short-term react-and-respond cycle.
When planning performs risk-mitigation activities in isolation, other functional areas can be adversely impacted. For example, engineering, procurement, supplier quality, manufacturing, sales and finance may have to take reactive measures in their own silos that may negatively impact overall supply chain performance.
Direct Materials Management
The direct materials team often responds to disruptions in a similar way. This team can be composed of procurement, R&D, engineering and supplier quality. It ultimately helps secure supply by taking specific supplier relationship management (SRM) actions and addressing attributes of the physical incoming goods. In isolation, direct materials reacts and responds with various mitigation options. Its teams engage in daily firefighting to ensure normal business continues, either by altering product research and development or reallocating purchases from suppliers.
For example, the direct materials team can work with suppliers to secure future supply, expedite orders, re-allocate supply to alternative suppliers and identify new suppliers. When demand is high and available supply from current suppliers is low, procurement might have to identify new sources of supply. If this is done without manufacturing or planning input, direct materials might continue to play catch-up and not be able to effectively address to supply base disruptions.
When supply is at risk due to supplier quality issues or global disruptions, direct materials can identify and use alternate suppliers, enable additional fulfillment channels, or expedite shipping depending on customer requirements. Engineering and supplier quality can focus on validating and managing specification conformance of the direct material, and identify engineering mitigation opportunities to leverage more modular designs and build flexibility for alternative parts.
Manufacturing
Manufacturing bears the brunt of disruption with supply shortages, receiving inputs from the planning organization and whatever supply the direct materials organization can secure. It consequently may continually have to replan production based on inventory or labor availability and capital equipment capacity.
Manufacturing organizations must work hand-in-hand with the planning and direct materials teams to update the production plan based on changing demand, shifting supply or inventory availability, and logistics challenges. Many times, manufacturing doesn’t have visibility into supply availability. This visibility from direct materials and planning is crucial to manufacturing’s ability to rebalance or revise the production plan. Additionally, manufacturing must work together with R&D, engineering, and supplier quality to evaluate and implement changes to the product bill of materials (BOM) if certain components aren’t available. Manufacturing also can deploy postponement options, delaying the full product build until the most opportune time to maintain standardization deep into the manufacturing process, after which more custom features can be included.
The cornerstone to maintaining continuity of supply and creating a resilient supply chain is to drive alignment across multiple business groups, to bring transparency to the supply chain. Using these strategies, the supply chain network can make the leap from short-term react-and-respond to a predict-and-manage structure. Organizations will see improved planning forecasts and manufacturing schedules. Single functions aren’t able to manage supply risk effectively in a silo. A coordinated effort across planning, direct materials, and manufacturing will drive decision-making and ensure continuity of supply.
Organizations will need to manage their supply chain network less like a cost center and more like a continuous value-generation engine. People, process and technology all play a key role in continuously improving the supply chain and reducing disruptions to establishing cross-functional alignment and supply chain resiliency.
With greater supply chain visibility and functional alignment, organizations no longer need to operate in “chaos mode,” continually reacting to the present daily emergency to secure supply to meet demand. Instead, they can break the cycle and develop the predict-and-manage capabilities that can turn disruptive events with significant business impacts into more industrialized risk-mitigation outcomes.
Connor Stewart is senior manager, and Adam Robbins is principal director, with Accenture.