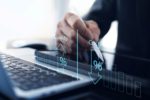
At its core, sales and operations planning (S&OP) has one simple goal: Allocate resources to match supply and demand. But that's easier said than done.
S&OP is often stymied by unreliable data, information silos, and scheduling challenges. Technology solutions promise to improve and streamline the process, and most organizations expect to invest more in S&OP tech in 2019.
S&OP technology has evolved from a priority to a necessity. A recent APQC survey found that 76 percent of those surveyed expect to invest more in S&OP tech in 2019 compared to 2018, and 69 percent say that technology is a critical part of their S&OP process. Respondents pointed to several drivers of the imperative to adopt S&OP tech: better data management, the ability to derive actionable insights from data, and the need to achieve multidimensional goals.
Cloud computing and collaboration tools are the most widely-used technologies in the S&OP process, and with good reason: these technologies bring big benefits at a minimal cost. One of the main strengths of cloud computing is the ability to increase storage and processing power on demand without the delay and expense of acquiring hardware that is often only needed for short periods of time. Cloud also helps organizations integrate data from disparate sources, thereby improving the transparency and scalability of S&OP. The vast majority (94 percent) of organizations surveyed by APQC use cloud in their S&OP processes. Collaboration tools like Slack, Basecamp and Office 365 are also popular technology enablers for S&OP. These tools improve productivity and give leaders quicker insight into resource availability. APQC found that 64 percent of organizations use collaboration tools for S&OP.
Analytics is also gaining traction in S&OP. Used by 52 percent of those surveyed by APQC, analytics tools turn “big data” into actionable insights for demand forecasting, price management, inventory management, scenario modeling and market trend analysis. AI and IoT take this a step further by tracking inventory, expenditures, key performance indicators and disruptions in real time. However, these technologies are not yet widely used for S&OP: 26 percent of respondents use IoT and 21 percent use AI.
Supervisory control and data acquisition (SCADA) software allows organizations to monitor and control manufacturing and production processes with little human input, freeing up employees for value-added work. This technology promises great benefits but can also create security vulnerabilities. Cyber criminals know one way to disrupt an organization is to attack its SCADA system. Only 41 percent of those surveyed report using SCADA. This is unsurprising, given that APQC also found that reliability and security are organizations’ foremost concerns about implementing new technology. SCADA is a must-have for large manufacturers, but smaller organizations often choose to avoid its potential risks.
To successfully integrate any technology into S&OP, supply chain leaders will need to define use cases, selection criteria, and potential implementation barriers. Despite most organizations’ willingness to invest, APQC found the biggest obstacles to adoption are budgetary constraints and a lack of consensus about how to move forward. Supply chain leaders will need to reach across the organization to secure budget and buy-in.
The Outlook
Low-cost, user-friendly, and easy-to-implement technologies like cloud and collaboration tools are commonplace in the S&OP space. However, there is a bigger gap between the haves and have-nots when it comes to the leading-edge technologies—such as AI, IoT, and SCADA—that are most relevant for achieving truly effective, streamlined and strategic S&OP. Companies are prepared to make technology investments in 2019, and supply chain leaders must capitalize on this crucial moment of opportunity.
Ryan Sullivan is a research analyst at APQC. Mercy Harper is a writer at APQC.
RELATED CONTENT
RELATED VIDEOS
Timely, incisive articles delivered directly to your inbox.