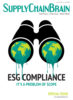
And getting tougher. Think of the laundry list of product-safety regulations with which manufacturers must comply today: the U.S. Consumer Product Safety Improvement Act (CPSIA), the European Commission’s Registration, Evaluation, Authorization and Restriction of Chemicals (REACH) regulation, Europe’s Restriction of Hazardous Substances (RoHS) directive, California’s Proposition 65 on environmental health hazards, and strict product standards in the U.K. and China, to name a few.
The massive number of product recalls suggests that companies are doing an imperfect job of keeping pace with quality requirements. Most recently, we’ve seen the recall of bicycles, baby coveralls, flashlights and hooded jackets. They are far from atypical in their number and variety. According to an index published by Stericycle, Inc., 21.3 million units of product were recalled in the U.S. in the fourth quarter of 2013 – an increase of 292 percent over the previous quarter.
The reasons are usually safety related, but they don’t have to be. A company might pull back a product for quality issues or relatively minor effects such as skin rashes. Recalls can be both mandatory and voluntary, in the latter case because the incident threatens to undermine the integrity of a brand.
It’s not so much a matter of product quality getting worse. The problem lies in the growing volume and complexity of regulations, says Keri Dawson, vice president of industry solutions and advisory services with MetricStream. Her company specializes in services for governance, risk and compliance.
As companies become more global, their operations move across national boundaries and jurisdictions. So, too, do the opportunities for violating local standards increase.
Dawson says the overall health and safety of consumer products have improved “dramatically” over the last few decades. Yet the need to ensure product quality worldwide, and handle the inevitable flood of recalls, is as strong as ever.
Companies these days are doing a somewhat better job of reacting to recall situations, Dawson says. Leaders have taken proactive steps toward creating more transparent supply chains, tracing the contents of food or finished goods all the way back to the source. “It’s critical to know every step along that product’s lifecycle,” she says, “so that you can make a determination of where the failure occurred.”
Retailers and manufacturers must be quick to act, even if erring on the side of safety. Between 2009 and 2013, the McNeil Consumer Healthcare unit of Johnson & Johnson recalled tens of millions of containers of Tylenol, Motrin, Benadryl and other popular over-the-counter remedies due to faulty manufacturing processes. The result was severe shortages at major drugstores.
“The manufacturer took no chances and recalled everything,” says Dawson. “Many analysts in hindsight have said that their willingness to do that was critical to not undermining the Tylenol brand.”
Food safety is a whole other can of worms, if you’ll pardon the phrase. Enactment of the Food Safety Modernization Act (FMSA) at the beginning of 2011 saddled producers with a much tougher compliance regime. Dawson calls it “one of the most significant recastings of food-safety requirements in the U.S. in many, many years.”
Then there are the product-content issues that are potentially life-threatening, such as untreated children’s clothing that can catch fire, coupled with recent studies showing that flame-retardant chemicals are themselves dangerous to the wearer.
For all their diligence at brand protection, many manufacturers have yet to achieve the level of visibility into their supplier bases that’s needed to prevent quality failures, and deal with them when they do occur. “Most organizations have gotten so complicated that it is extremely difficult to maintain adequate levels of control across the totality of the supply chain, including manufacturing and distribution,” says Dawson.
Add to that the prospect of misbehavior by suppliers, who might cut corners to preserve profit margins, or maintain inhumane working conditions in factories thousands of miles from the buyer. Then it becomes more than a question of a single faulty product. When a factory complex collapses and kills 1,129 workers, what kind of a recall can fix the problem?
It’s all about visibility and collaboration, or the lack of it. Dawson says many companies still maintain separate buying and sourcing organizations that don’t interact with one another, let alone with manufacturing and distribution. “They aren’t necessarily coordinated or working from the same body of knowledge.” It’s no wonder that poor or dangerous products occasionally slip between the cracks.
The first step toward achieving true visibility is to make use of the data that already exists, Dawson says. Look at the company’s history of recalls and analyze what happened. Utilizing hindsight, the exercise should uncover warning indicators that can be built into current risk-management systems.
“There are two things you’ll need,” Dawson advises. “The ability to identify events that are leading indicators of a potential recall event, and sufficient transparency across that product’s lifecycle. Where did it come from? What distribution path was followed? Figure that out, and you have a jump-start about that product, and where the failure occurred.”
Next, companies need to put into place a good communication plan – one that draws on the power of social media, which can provide near-instantaneous information about an incident. Armed with such intelligence, a manufacturer or retailer can address the problem while simultaneously dealing with the publicity fallout. “One of the worst things you can do is say nothing,” says Dawson, noting General Motors’ alleged delay in responding quickly to reports of faulty ignition switches in several models of its cars.
Companies can move away from “siloed” behavior through the use of a common technology platform that ranges across the organization, and upstream to suppliers as well. “You’re never going to merge into one mega-group,” says Dawson, “but you do need to make sure that the leaders of those teams understand the interplay [of processes].”
It’s a move that companies, particularly in the Fortune 500, are just beginning to make. “They’re in a much different state now than a year and a half ago,” says Dawson. “A year and a half from now, we will see a dramatic step-change.”