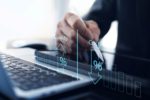
Nearly three years after the onset of the COVID-19 pandemic, the industrial sector is still facing persistent supply chain and logistics challenges. Trends like the rise of e-commerce and working from home have sent shockwaves throughout the commercial real estate industry, and driven skyrocketing demand for industrial space. Record low vacancy rates have businesses scrambling to find space, and with many tenants focused on preventing inventory shortage, warehouses are overstuffed.
The tightening of industrial real estate supply, coupled with overflowing inventory and rising rents, has made traditional warehousing an impractical solution for businesses attempting to navigate this new market. Even with record levels of industrial space under construction, most buildings are pre-leased before construction has even started, and high net absorption rates means construction can’t come fast enough.
With the holiday season right around the corner, many businesses have found it difficult to plan ahead, making it especially important for those that have faced disruptions to daily operations to stay adaptive to market conditions. Tenants must be strategic in how they approach warehousing, to ensure they’re finding the space that best fits their needs.
What businesses struggling to find space might not know is that, despite extreme supply constraints, there are large portions of industrial real estate in the market sitting vacant and underutilized. These hidden gems can be leveraged as short-term, on-demand warehousing to help alleviate common pain points felt by businesses and industrial real estate owners. For companies that need to stay agile amid constantly changing factors impacting inventory, customer experience and demand, these cost-effective, short-term warehousing solutions can be a lifeline.
A huge upside for businesses taking advantage of on-demand warehousing is the significant cost savings that result. As the gap between supply and demand grows, the vacancy squeeze will continue to push rents higher, making it difficult for companies that can’t predict what their inventory will look like from one month to the next to afford long-term leases. Extra industrial space that goes unused is a huge financial strain for a business, especially with a looming recession. On the other hand, purchasing patterns are still so unstable from the pandemic that overflow is also a financial concern. Utilizing on-demand warehousing gives a business maximum flexibility in length of lease, cutting down costs and allowing it to remain profitable through tumultuous times.
Short-term warehousing has also become a go-to for many businesses shifting to the just-in-case (JIC) supply chain model, in an attempt to avoid delays and shortages during the upcoming holiday season. As more companies abandon the just-in-time (JIT) model, they need a quick and flexible option to store extra inventory. Because most short-term warehousing options are on-demand, businesses can reserve space almost immediately for the time and place they need it, without the added pressure of having to sign binding contracts or long-term leases. Additionally, the versatility of on-demand warehousing means that it can provide support to a variety of businesses for a variety of reasons – whether a retail company needs space for extra inventory, or a construction company needs temporary storage for a project nearby.
On the supply side, owners can turn pockets of unused space into revenue while helping businesses secure the space that best suits their fluctuating needs and timelines amid ongoing logistics issues. On-demand warehousing was created with the goal of being adaptable, and oftentimes the space available might not be traditional industrial real estate. For example, owners of vacant department stores can list this space on an on-demand warehousing platform, to turn a profit on what otherwise would have been an underutilized asset. During a time when supply is rapidly becoming scarce, even the most unconventional warehouses can prove to be necessary resources for companies desperately in need of space.
It’s more important than ever for businesses to be prepared for any possible scenario. The pandemic has proved that any number of events can upend day-to-day operations with little to no warning. Agile businesses are creating contingency plans in the form of on-demand, short-term warehousing. Not only do such facilities provide needed space, they offer companies the luxury of planning ahead in the face of ongoing market volatility.
Brad Wright is chief executive officer of Chunker.
RELATED CONTENT
RELATED VIDEOS
Timely, incisive articles delivered directly to your inbox.