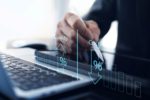
Photo: iStock.com/greenbutterfly
Companies need a new approach to managing their supply chains. With the COVID-19 pandemic, the post-pandemic phase, and now soaring inflation, every industry has been impacted by changing consumer behaviors, labor shortages, material and transportation cost increases and, in some cases, country shutdowns.
In the face of these factors, both just-in-time and just-in-case strategies can be too costly, either through lost sales or excess inventory. Manufacturers, distributors and retailers need to pivot to a smart just-in-telligent methodology, blending just-in-time and just-in-case with the science of artificial intelligence (AI) and automation.
Greater Demand Accuracy
First and foremost, the demand signal needs to account for all possibilities ranging from everyday sales, trends and seasonality, to promotions/events, to external market factors. What happens when consumers cut spending, either in a pandemic or due to inflation? AI can automatically answer these questions and others, including which products are prioritized, which are necessities, and which are nice-to-haves. When disruptions occur, missed sales and unexpected spikes in demand should be smartly corrected, ensuring the demand picture accurately reflects what would have normally been sold.
AI-based machine learning is a modern model that helps companies automatically access and understand weekly selling patterns. Whether the product is paper, food and beverage, electronics, or pharmaceuticals, each has a story to tell in its sales history. Knowing these patterns makes companies better equipped when faced with market challenges.
Extending demand down to the customer level will help further improve accuracy by collaborating with sales teams to identify their growing or shrinking customer base plus upcoming orders.
Just-in-time allows for no variation in demand while just-in-case eats up profits via excess inventory. A just-in-telligent approach will smartly consider which products should have increased investments or less safety stock. Using demand volume and volatility as factors, inventory strategies can be tailored to deserving high-volume/low-volatility products while reducing stock levels of harder-to-predict, slower-moving SKUs and raw materials.
More Optimal Supply Chain
With an accurate demand signal, an optimized supply chain should be created with an AI-based optimization model that considers many factors and constraints throughout the network. Just-in-time minimizes inventory to match demand but will strangle a company’s ability to be flexible. Just-in-case builds inventory to prevent stockouts due to demand fluctuations upward, but carrying the extra inventory is expensive. A just-in-telligent approach is the ideal way to balance the need for additional inventory in some product lines with minimal inventory while smartly considering both supply costs and profitability.
The demand forecast and inventory strategies mentioned earlier record where the business wants and inventory bets are placed. But how should capacities like facilities, work centers, labor, and storage be respected? How do ever-increasing costs related to energy, transportation, packaging and the many raw materials affect business? What about reduced availability of key commodities either through transportation delays, labor shortages, country shutdowns or environmental factors? The sheer number of variables is overwhelming for people and for ERP-based material requirements planning (MRP) systems. AI-based linear programming models can automatically make the most financially sound decisions by simultaneously considering a variety of inputs to generate an optimized weekly or daily manufacturing, purchasing or transfer supply plan. That’s a huge help.
In some cases, organizations may want to test out different factors that allow planners to evaluate the financial implications of alternate transportation modes, alternate sources of supply, alternate manufacturing plants or lines and even the impact of future price increases. Scenario planning will invoke the optimization models in a workspace before making final network decisions that automatically play out in the weekly supply plan.
Running a just-in-telligent supply chain will benefit all aspects of the business by producing optimal orders, along with providing future visibility into where problems can be anticipated and resolutions established in advance. When all aspects of the supply chain are at optimal levels, raw material wastage is reduced and excess capacity can be exploited for additional revenue and profits.
More Optimized Manufacturing Production Schedule
The just-in-telligent concept also applies to production and the shop floor. With the optimized weekly or daily manufacturing orders created, the next job is to sequence the work across the days or within the hours/minutes of a day for each work center. Many schedulers manually sequence orders, with only a few considerations. The amount of data to be examined is overwhelming.
An AI-based optimization model will help automate the scheduling and allow schedulers to manage by exception. Sequencing rules with changeover times in the model will address allergens, light to dark, packaging size, changes in brands and much more, ensuring that every schedule minimizes changeover costs and maximizes time efficiencies. The constant challenge to synchronize equipment, tanks, tools, materials, and labor is addressed with optimization.
When unplanned downtimes occur, a just-in-telligent technique will automatically re-sequence the schedule to balance the batches across lines, resources, and labor shifts to move orders forward and backward as needed to accommodate the downtime and minimize changeover.
What-if scenarios are critical for measuring the impact schedule changes may have on production lines. Schedulers engage in visual tools to drag/drop changes, view impacts on cost/time, report on performance, even manually place orders on the board if desired. After studying the consequences of modifications, the scheduler can promote the new schedule to the shop floor.
By embracing a just-in-telligent path, manual processes resulting in delays in schedules, idle machines, line congestion, quality issues or late-delivery penalties are eliminated, delivering more profits to the business.
Regardless of industry or type of business, a just-in-telligent approach which takes advantage of AI and automation will unlock enormous value throughout complex supply chains. On top of this foundation, organizations can stack process improvements like sharing perspectives and projections through collaboration with customers and suppliers, as well as supplier diversification, to minimize disruptions and achieve overall risk reduction.
The charge to you is to embark on a just-in-telligent journey that will lead to a better balance of financial returns, inventory investments, resource utilization and risk reduction, ending with greater customer satisfaction — a win-win for all!
Michael Dale is senior director of retail strategy at Infor.
RELATED CONTENT
RELATED VIDEOS
Timely, incisive articles delivered directly to your inbox.