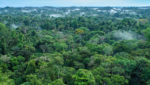
Only a year ago, the mere mention of a “virus” would have evoked in many people’s minds the image of a sick computer. Now, with the word having shed its metaphorical skin, and a literal virus posing a deadly threat to humans the world round, it’s robots to the rescue.
That, at least, is how the world of e-commerce distribution views the current labor scene, when it comes to staffing up to handle consumer demand during the holiday shopping peak. On top of the usual need for extra hands is the requirement for strict social distancing in the workplace. (Assuming that employees are in the workplace at all.) With the coming of colder weather, fears of a second wave of COVID-19 have many warehouse operations wondering whether they can hire enough people to do the job.
It's more than a matter of finding workers to fill each position. According to inVia Robotics, a specialist in warehouse automation, companies hire an average of three times the amount of seasonal help they ostensibly need, to cover no-shows, sick days and, now, COVID-19 restrictions. There’s even a growing call for distribution expertise within retail stores, which are converting portions of their floor space into micro-fulfillment centers to handle orders received over the internet. Robots might hold the answer.
Automation, of course, was well advanced in the warehouse world long before COVID-19 came along. The trend can be traced all the way back to the late 19th century, with introduction of the conveyor belt. But today’s distribution robots are a different animal entirely, aping the actions and thought processes (if not actual thoughts) of humans. They can direct workers where to find multiple products for picking in the racks, then convey those items to the loading dock. Some do the picking themselves. Most of all, they reduce the amount of physical distance in the warehouse that humans must cover, which depending on the operation can range anywhere from five to 12 or more miles per day.
Lior Elazary, chief executive officer of inVia Robotics, breaks down the evolution of robots in the warehouse into five distinct stages:
The coming of the coronavirus pandemic has only accelerated progress toward automation that was already underway. Even with unemployment spiking, people are becoming an increasingly rare asset. “Every one of our customers has had a COVID case in their warehouse, and has had to shut it down,” Elazary notes. But in a time of quarantine, robots can keep right on working.
“Lights-out” warehouses, where humans are completely absent, exist today in certain parts of the world. But they’re expensive to run, and suitable only for handling select merchandise in countries where human labor is either lacking or especially expensive. Even with arrival of the fifth stage of robotic evolution, Elazary doesn’t see a complete end to human labor in a warehouse setting — just its repurposing, well beyond the execution of boring and repetitive tasks.
In the short term, more robots are a solution to the pandemic-induced worker shortage and looming peak season. “You get throughput without having to introduce tremendous amounts of labor,” Elazary says. “Before, you needed 400 to 500 extra people. And you’d have to hire 1,000 to 1,500 just to end up with 500 doing the work. That was a huge pain point.”
And what of peak season’s end, when those hundreds of temp workers are unceremoniously cut loose? Will robots face the same fate, ending up in some storage shed until the next holiday surge? Automation experts have worked hard to prevent that scenario from occurring. Many of today’s robots are designed for flexibility, so in slow periods can be redirected to perform tasks like replenishment, cycle counting and optimization of inventory placement.
This holiday season and beyond, expect to see growing armies of robots in material-handling roles, from micro-fulfillment operations to massive distribution centers. It didn’t require a pandemic to get the automation ball rolling. Nor will it need one to fulfill automation’s long-term promise.
RELATED CONTENT
RELATED VIDEOS
Timely, incisive articles delivered directly to your inbox.