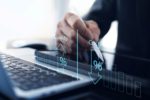
It’s no surprise that consumers are conducting their holiday shopping online just as much, if not more, than in store - but they’re also starting earlier. In fact, e-commerce on the weekend leading up to Cyber Monday was up 17 percent this past year, compared with the same weekend in 2013, according to IBM. Having already done their research, consumers know what they want and where to find the best deal.
With consumers procrastinating less, companies that want their products wrapped and ready for the holidays need to start earlier as well – even as early as 12 months ahead of time. In actuality, in a well-performing supply chain, when the consumer clicks buy, the product is already nearing the end of its journey. To do this successfully and not return an “out-of-stock” message to consumer searches, a visible supply chain is necessary.
Let’s explore what the best practices of a supply chain should be and how striving to replicate these practices can help ensure your product will be ready in time for December.
• Six to twelve months in advance: The company has considered volume forecast and is exploring market demand. They’re determining capacity at factories and working with vendors of long-lead-time materials to decide if they have product ready and can commit to the timeline.
Certain products are more complex than others, such as electronic products. Products’ intricate parts and multiple origins can cause supply chain issues if not properly monitored. An extra time buffer is needed for advanced planning and scheduling. Although the product team might know what they want to do – such as build 100,000 cameras – advanced planning tools help determine when and how many products must be assembled, how many and what kind of materials need to be ordered, what colors customers might demand and which countries to supply. The more detail that can be added to the forecasting plan, the more success the product team will see leading up to the execution date.
A lesson to be learned here is to not fully assemble your products 12 months out. This is a pattern that the industry needs to break. It’s too dangerous to commit to resources that far in advance; product surplus and revenue loss can become serious concerns. The key is finding the sweet spot – not too far in advance and not too late.
Instead, this switch to “just in time” production schedules enables product teams to fluidly adapt to market fluctuations, recall orders and make upgrades as needed to existing products to help shorten production lead times.
• Three to six months before the consumer clicks 'buy': Timing is crucial to ensure the capacity needed will be accurately reflected when consumers begin to select their purchases. During this time, the more granular details should be worked out, such as desired product specifications, including screen size and if there will be touch screen capabilities. These details must be ironed out with suppliers to ensure materials and manufacturing assets will be available in time.
• One to three months before the holiday rush: Products make their way to the warehouse where short-lead-time materials and region-specific items are purchased, while appropriate languages are added to the product – all based on forecasting and insight into regional demand. In addition, as early as possible, companies should work with their shipping partners to book available services and avoid last-minute budget-killers like having to airship product versus shipping by sea.
• Two to four weeks out: The product is assembled and ready for distribution. Access to real-time calculations can determine whether a product is available or faces severe delay, ultimately resulting in revenue loss. In this phase, sales teams must provide feedback about demand and warehousing solution providers must provide insights into capacity. Continuous feedback between all parties can help ensure the proper availability of the end product.
• Purchase Time: Ideally, by the time a customer puts a product in their online cart, inventory is already checked so that customer satisfaction ratings are not jeopardized if that product is, in fact, unavailable. Today’s customers are more educated when making purchases and are willing to bring their loyalty elsewhere if what they want is unavailable on your site, handing your profit over to your competitors.
During the holidays, another important part of the process is personalization. This must be done quickly, efficiently and effectively to ensure customer satisfaction. Once the purchase is made, if customization is requested, the unique attribute can be added, such as a name or engraving – and then the piece is moved to shipping. A key aspect to a visible supply chain during this last mile of the product’s journey is ensuring that customers receive real-time updates based on their preferences.
When all is said and done, even with a bullet-proof plan, catastrophe can still occur. Disasters like factory and port strikes, lost containers or natural disasters can derail even the most fluid supply chain. The key is immediately mobilizing and enacting your disaster recovery plan, one that can prevent products from being stuck at port. By keeping your disaster recovery plans up to date, you can be adaptable – having the ability to move product from one place to another if needed, avoiding loss of revenue.
Though many of us may wish the hectic holiday season would stay behind us, the fact is that in order to foster a resilient and visible supply chain for the next holiday season, you must start preparing immediately. Communication, early preparedness and a stable supply chain partner can ensure products arrive in time for the 2015 holidays, while keeping your business profitable.
Source: ModusLink
RELATED CONTENT
RELATED VIDEOS
Timely, incisive articles delivered directly to your inbox.