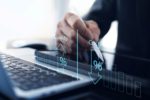
Smart technology is rewriting the book for what’s possible in supply chain management as a profit driver.
Big data analytics, internet of things (IoT) sensor data inputs, artificial intelligence (AI), decision engines and data standardization can now provide a single, global “version of the truth” about what’s going on in the supply chain, what may occur, and what to do about it. These applications layer on real-time visibility plus decision-making functions and smart analytics — all bundled in a supply chain control tower — to deliver powerful, bottom-line results.
These emerging technology and analytics capabilities are known as Supply Chain 4.0. When successfully and fully executed, SC 4.0 drives proven profitability improvement. But there’s a big qualifier in this statement. Most businesses deploy SC 4.0 in their forward supply chain — i.e., the supply chain that delivers new product to customers.
That leaves one enormous supply chain completely under-served by SC 4.0: the after-sale/support supply chain.
Front and Center
For years, the after-sale/support supply chain has been the poor stepchild to the forward supply chain.
“Most companies have focused their supply chain optimization efforts almost exclusively on the forward supply chain,” says Mike Wooden, chief executive officer at OnProcess Technology, a managed services provider specializing in optimizing the post-sale supply chain.
“But that’s changing — fast. The industry is making progress in transforming the relatively ‘backward’ post-sale supply chain, rapidly making investments to bring it up to par with its sophisticated forward supply chain ‘brother’. This is especially true in sectors where companies must service high value, super-critical assets and infrastructure.”
Take infrastructure technology OEMs, for example. These companies face tremendous pressure from their customers to reduce costs, all the while providing high levels of infrastructure uptime and reliability. To compete, these tech OEMs continuously strive to improve the customer experience in an environment where these same customers pretty much expect — and demand — 100 percent uptime and reliability.
But the two prime objectives, controlling cost and providing high service levels, often conflict. And because of underdeveloped post-sales/support supply chains, OEM service organizations are often regarded as cost centers. This cost-center affiliation results from frequently-missed service-level agreements (SLAs) that not only incur expensive penalties, but also frustrate customers, increase inventory carrying costs, and in worst-case scenarios, result in customer defection to a competing provider.
“It’s very hard for tech OEMs to optimize their complex service operations,” Wooden observes. “For one thing, like all companies, they must prioritize their resources. Typically, the forward supply chain receives the bulk of resource attention, leaving the service supply chain under-funded and sub-optimized.
These OEMs also often lack the end-to-end visibility needed to manage a best-in-class post-sale value chain. Why is this? One big reason: They are inundated with data from multiple internal and external information systems. The internal systems are almost always siloed, so getting a real picture of the after-sale service operation is tremendously challenging. And the external systems are highly variable in systems and platforms, making the data they generate difficult to integrate within the OEM data ecosystem.”
But research shows that short-changing the after-sale supply chain carries a huge lost-opportunity cost. According to a landmark Bain & Company study, investing in the after-sale service supply chain can generate a 4 percent increase in revenue rates, and a 12 percent improvement in gross margins. For some companies, these numbers are even higher. Leading manufacturers like Ford and Caterpillar know this and have been investing internally for years in after-sales supply chain systems.
Without appropriate investment and strategic attention, the after-sale service supply chain remains a manually managed operation that is not only costly but can result in diminished competitive advantage.
The Intelligent Post-Sale Supply Chain Control Tower
Ideally, the goal of the after-sales service and support supply chain is near 100 percent asset up-time and/or meeting the agreed-upon customer SLAs for asset uptime, recovery, repair, etc.
But how do you use SC 4.0 technologies to help realize these commitments on a more assured basis — especially if your organization has been historically reluctant to invest in such systems? How do you turn post-sale service from a cost- to a profit-center? One answer: An outsourced service supply chain, powered by an intelligent control tower.
Just what is a post-sale supply chain control tower?
“An intelligent after-sales service management control tower is not a passive dashboard with flags telling you something has gone wrong,” says Sarah Hatfield, vice president of product and marketing at OnProcess Technology. “It is far higher on the maturity scale. It incorporates big data analytics, artificial intelligence, internet of things inputs and other technologies, and uses them to orchestrate optimal service operations.”
The intelligent control tower aggregates and standardizes data from many disparate data sources — e.g., company systems of record, suppliers, vendors, partners — to create a single view of what’s occurring in the service supply chain, what’s likely to happen and when, what to do about it and when. It is proactive, predictive and automated.
“Crafting this level of supply chain maturity is not easy,” Wooden notes. “It requires orchestrating service technicians, parts inventory, suppliers, engineers, transportation, and the technology to keep track of and manage these internal and external moving parts.”
Climbing the Maturity Ladder
Because of this level of complexity, after-sales service control towers, much like supply chains in general, vary widely in sophistication. They tend to develop along a maturity continuum or ladder, with discrete, additive stages of capabilities. According to Hatfield, there are five such stages:
Stage 1: Visibility dashboard. Control towers provide visibility into what’s going on or what has happened in the after-sale supply chain. Data are collected from disparate sources, internal and external, and aggregated into a singular view. Even in its simplest form, this level of visibility has tremendous value. “If you can’t see what’s going on — you don’t know what problems you’re facing,” observes Hatfield.
Stage 2: Real-time insight. Real-time data enables companies to operate more effectively and efficiently, with an accurate picture of what is occurring, as it occurs. With real-time data, a company can identify and resolve an issue as soon as it arises.
Stage 3: Embedded analytics. Embedding analytics within the control tower enables trend identification and analysis, generating new, previously unknown data insights. “By this stage, you start realizing significant, differentiating value from a less mature control tower,” Hatfield notes.
Stage 4: Artificial intelligence. This stage adds predictive analytics and machine learning to recommend alternative courses of action. AI also can identify new opportunities for savings or improvements.
Stage 5: Process automation. In stage 5, the intelligent control tower automates service decisions based on decision-tree style business rules, determined through the predictive analytics and machine learning findings generated in stage 4. This automation enables faster, accurate, cost-effective responses to customer needs. While efficiencies associated with automation generate significant benefits in and of themselves, the real value of a Stage 5 intelligent post-sale control tower derives from markedly increased service quality, and process optimization. The results drive directly to increased profitability.
Bottom-Line Impact
A stage 5 intelligent control tower and outsourced service supply chain is a tremendously valuable asset when it comes to supporting the service value chain. “It is about being proactive, and delivering unparalleled business outcomes, rather than being in constant reactive mode,” says Wooden.
‘Intelligent control towers help transform how companies provide after-sale product support to their customers,” he says. “How well a business accomplishes this job ties directly into customer satisfaction — whether the customer is happy, buys again from the company, or defects to a competitor.”
The potential value proposition from implementing this kind of platform makes CEOs sit up and pay attention. Wooden says, “I can go into a large company and tell them, ‘I can save you $25m annually.’ And I can prove that result.”
RELATED CONTENT
RELATED VIDEOS
Timely, incisive articles delivered directly to your inbox.